388. Для температур выше 200 градусов Цельсия давлением до 25 Мегапаскаль (250 килограмм силы на сантиметр квадратный) применяется прографиченная асбестовая набивка, (кольцо покрыто слоем сухого чистого графита толщиной не менее 1 миллиметра).
389. Для высоких температур применяются специальные набивки, в частности асбометаллические, пропитанные особыми составами, стойкими к разрушению и вытеканию под влиянием транспортируемой среды и высокой температуры.
390. Для давления свыше 32 Мегапаскаль (320 килограмм силы на сантиметр квадратный) и температуры более 200 градусов Цельсия применяются специальные набивки.
391. Сальниковые набивки арматуры изготавливают из плетеного шнура квадратного сечения со стороной, равной ширине сальниковой камеры.
392. Кольца набивки укладывают в сальниковую коробку, смещая линии разреза и уплотнение каждого кольца. Высоту сальниковой набивки принимают такой, чтобы грундбукса в начальном положении входила в сальниковую камеру не более чем на 1/6 - 1/7 ее высоты, но не менее чем на 5 миллиметров.
Сальники подтягивают равномерно без перекоса грундбуксы.
393. Для обеспечения плотности сальникового уплотнения проверяется чистота поверхности шпинделя и штока арматуры.
394. Прокладочный материал для уплотнения соединения крышки с корпусом арматуры выбирать с учетом химического воздействия на него транспортируемой среды, в зависимости от давления и температуры.
395. Ход шпинделя в задвижках и вентилях плавный, а затвор при закрывании или открывании арматуры перемещается без заедания.
396. Предохранительные клапаны обслуживаются в соответствии с технической документацией.
397. Не допускается применять добавочные рычаги при открывании и закрывании арматуры.
398. Ревизию и ремонт трубопроводной арматуры, в том числе и обратных клапанов, приводных устройств арматуры (электро-, пневмо-, гидропривод, механический привод) производят в период ревизии трубопровода.
399. Ревизию и ремонт арматуры производить в специализированных мастерских или ремонтных участках. Ревизия арматуры путем ее разборки и осмотра проводится на месте установки (приварная арматура, крупногабаритная и труднодоступная) с обеспечением необходимых мер безопасности.
400. При ревизии арматуры, в том числе обратных клапанов, выполняются следующие работы:
1) визуальный осмотр;
2) разборка и осмотр состояния отдельных деталей;
3) осмотр внутренней поверхности контроль неразрушающими методами;
4) притирка уплотнительных поверхностей;
5) сборка, опробование и опрессовка на прочность и герметичность.
401. При планировании сроков ревизии и ремонта арматуры в первую очередь проводить ревизию и ремонт арматуры, работающей в наиболее сложных условиях. Результаты ремонта и испытания арматуры оформляются актами и заносятся в эксплуатационную документацию.
402. Когда характер и скорость коррозионного износа трубопровода не установлены типовыми методами контроля, используемыми при ревизии, для контроля приближения толщины стенки к отбраковочному размеру выполняются контрольные засверловки.
403. Трубопроводы, по которым транспортируются вещества группы А(а), А(б), газы всех групп, трубопроводы, работающие под вакуумом и высоким давлением свыше 10 Мегапаскаль (100 килограмм силы на сантиметр квадратный), трубопроводы в блоках I категории взрывоопасности, трубопроводы, выполненные из аустенитных сталей и работающих в средах, вызывающих межкристаллитную коррозию, контрольным засверловкам не подвергают. В этих случаях устанавливается контроль за состоянием толщины стенок трубопровода путем замера ультразвуковым толщиномером.
404. При засверловке контрольных отверстий пользоваться сверлом диаметром 2,5-5 миллиметров, заправленным под острым углом.
405. Отверстия при контрольных засверловках располагать в местах поворотов, сужений, врезок, застойных зонах, в тройниках, дренажных отводах, перед запорной арматурой и после нее.
406. Отверстия контрольных засверловок на отводах и полуотводах располагать по наружному радиусу гиба из расчета одно отверстие на 0,2 метра длины, но не менее одного отверстия на отвод или секцию сварного отвода.
407. Глубина контрольных засверловок устанавливается равной расчетной толщине трубопровода плюс П×С (где П - половина периода между очередными ревизиями, год, С - фактическая скорость коррозии трубопровода, миллиметра в год).
408. Места расположения контрольных засверловок на трубопроводе четко обозначаются и фиксируются в документации.
409. Пропуск контрольного отверстия на трубопроводе, показывает приближение толщины его стенки к отбраковочному размеру, такой трубопровод подвергается внеочередной ревизии.
Пункт 410 изложен в редакции приказа Министра по чрезвычайным ситуациям РК от 17.01.23 г. № 24 (введен в действие с 3 февраля 2023 г.) (см. стар. ред.)
410. Периодические испытания трубопроводов на прочность и герметичность проводят во время проведения ревизии трубопровода.
Сроки проведения испытания для трубопроводов с давлением до 10 Мегапаскаль (100 килограмм силы на сантиметр квадратный) принимается равным удвоенной периодичности проведения ревизии, принятой согласно условиям пункта 367 для данного трубопровода, но не реже одного раза в 8 лет.
Сроки проведения испытания для трубопроводов с давлением свыше 10 Мегапаскаль (100 килограмм силы на сантиметр квадратный) не реже:
1) для трубопроводов с температурой до 200 градусов Цельсия - один раз в 8 лет;
2) для трубопроводов с температурой свыше 200 градусов Цельсия - один раз в 4 года.
Пункт 411 изложен в редакции приказа Министра по чрезвычайным ситуациям РК от 17.01.23 г. № 24 (введен в действие с 3 февраля 2023 г.) (см. стар. ред.)
411. Периодические испытания трубопроводов на прочность и герметичность проводят во время проведения ревизии трубопровода. Испытательное давление и порядок проведения испытания соответствуют допустимым условиям главы 7 настоящей Инструкции.
412. Результаты периодических испытаний трубопроводов оформляются актом по форме согласно приложению 21 к настоящей Инструкции.
413. Трубы, элементы трубопроводов и арматуры, в том числе литой (корпуса задвижек, вентили, клапаны), подлежат отбраковке, если:
1) при ревизии на поверхности были обнаружены трещины, отслоения, деформации, гофры, вмятины, вздутия;
2) в результате воздействия среды толщина стенки ниже проектной и достигла величины, определяемой расчетом на прочность без учета прибавки на коррозию (отбраковочный размер);
3) изменились механические свойства металла;
4) при контроле сварных швов обнаружены дефекты, не подлежащие исправлению;
5) размеры резьбовых соединений не соответствуют полям допусков или на резьбе имеются срывы витков, трещины, коррозионный износ;
6) трубопровод не прошел гидравлического или пневматического испытания;
7) уплотнительные элементы износились и не обеспечивают безопасное ведение технологического процесса.
Отбраковочные толщины стенок элементов трубопроводов и арматуры указываются в проектной документации.
414. Фланцы отбраковываются при:
1) неудовлетворительном состоянии привалочных поверхностей;
2) наличии дефектов;
3) деформации;
4) уменьшении толщины стенки воротника фланца до отбраковочных размеров трубы;
5) срыве, смятии и износе резьбы в резьбовых фланцах высокого давления, а также при наличии люфта в резьбе, превышающего допустимые пределы. Линзы и прокладки овального сечения отбраковываются при наличии трещин, забоин, сколов, смятин уплотнительных поверхностей, деформации.
415. Крепежные детали отбраковываются:
1) при появлении трещин, срыва или коррозионного износа резьбы;
2) в случаях изгиба болтов и шпилек;
3) при остаточной деформации, приводящей к изменению профиля резьбы;
4) в случае износа боковых граней головок болтов и гаек;
5) в случае снижения механических свойств металла ниже допустимого уровня.
416. Сильфонные и линзовые компенсаторы отбраковываются в следующих случаях:
1) толщина стенки сильфона или линзы достигла расчетной величины, указанной в паспорте компенсатора;
2) толщина стенки сильфона достигла 0,5 миллиметра, а расчетная толщина стенки сильфона имеет более низкие значения;
3) при наработке компенсаторами допустимого числа циклов с учетом условий эксплуатации на пожароопасных и токсичных средах;
Параграф 3. Техническая документация
417. Технологические трубопроводы комплектуются технической документацией. В состав технической документации входит:
1) проектная документация;
2) паспорт трубопровода и эксплуатационные документы:
3) наименование и адрес организации-владельца;
4) назначение;
5) дата изготовления (производства);
6) рабочая среда;
7) рабочие параметры рабочей среды: давление, Мегапаскаль (килограмм силы на сантиметр квадратный), температура, градусов Цельсия;
8) расчетный срок службы;
9) расчетный ресурс;
10) расчетное количество пусков;
11) схемы, чертежи, свидетельства и другие документы на изготовление (производство) и монтаж трубопровода;
12) утвержденные техническим руководителем организации схемы трубопроводов с указанием условного прохода, исходной и отбраковочной толщины элементов трубопровода, мест установки арматуры, фланцев, заглушек и других деталей, мест спускных, продувочных и дренажных устройств, сварных стыков, контрольных засверловок (если они имеются) и их нумерации;
13) акты ревизии и отбраковки элементов трубопровода;
14) сведения о качестве ремонтов трубопроводов, подтверждающие качество примененных при ремонте материалов, термической обработке сварных соединений трубопроводов, о качестве сварных стыков;
15) материалы по контролю металла трубопроводов, работающих в водородсодержащих средах;
16) акты периодического визуального осмотра трубопровода;
17) акты испытания трубопровода на прочность и герметичность;
18) акты на ревизию, ремонт и испытание арматуры;
19) эксплуатационные журналы трубопроводов;
20) акты отбраковки;
21) журнал установки-снятия заглушек;
22) паспорт арматуры.
Глава 9. Подземные трубопроводы
418. Для подземных трубопроводов устанавливается периодический контроль технического состояния.
419. Для ревизии подземных трубопроводов производят вскрытие и выемку грунта на отдельных участках длиной не менее 2 метра каждый с последующим снятием изоляции, осмотром антикоррозионной и протекторной защиты, осмотром трубопровода, измерением толщины стенок, а в обоснованных случаях с вырезкой отдельных участков.
Число участков, подлежащих вскрытию для ревизии, устанавливается в зависимости от условий эксплуатации трубопровода:
1) при контроле сплошности изоляции трубопровода с помощью приборов вскрытие производится в местах выявленных повреждений изоляции;
2) при выборочном контроле вскрытие производится из расчета один участок на 200-300 метров длины трубопровода.
420. При проведении ремонтных и монтажных работ на подземных трубопроводах устанавливается контроль, за выполнением условий проекта в части компенсации температурных деформаций, качества применяемых материалов, сварных швов, антикоррозионного покрытия и своевременного оформления документации по результатам проводимых работ.
421. Подземные технологические трубопроводы защищаются от почвенной коррозии и коррозии блуждающими токами.
Приложение 1
к Инструкции по безопасности при эксплуатации
технологических трубопроводов
Классификация трубопроводов давлением Ру≤10 Мегапаскаль (100 килограмм силы на сантиметр квадратный)
Группа | Транспортируемые вещества | Категория трубопроводов |
I | II | III | IV | V |
Давление Pрасч, Мегапаскаль (килограмм силы на сантиметр квадратный) | Температура tрасч, градусов Цельсия | Давление Pрасч, Мегапаскаль (килограмм силы на сантиметр квадратный) | Температура tрасч, градусов Цельсия | Давление Pрасч, Мегапаскаль (килограмм силы на сантиметр квадратный | Температура tрасч, градусов Цельсия | Давление Pрасч, Мегапаскаль (килограмм силы на сантиметр квадратный | Температура tрасч, градусов Цельсия | Pрасч, Мегапаскаль (килограмм силы на сантиметр квадратный | Температура tрасч, градусов Цельсия |
1 | 2 | 3 | 4 | 5 | 6 | 7 | 8 | 9 | 10 | 11 | 12 |
А | Вещества с токсичным действием | | | | | | | | | | |
а) чрезвычайно и высокоопасные вещества классов 1, 2 | Независимо | Независимо | - | - | - | - | - | - | - | - |
б) умеренно опасные вещества класса 3 | Свыше 2,5 (25) | Свыше 300 и ниже минус 40 | Вакуум от 0,08 (0,8) (абс) до 2,5 (25) | От минус 40 до 300 | - | - | - | - | - | - |
Вакуум ниже 0,08 (0,8) (абс) | Независимо | - | - | - | - | - | - | - | - |
Б | Взрыво- и пожароопасные вещества | | | | | | | | | | |
а) горючие газы (ГГ), в том числе сжиженные углеводородные газы (СУГ) | Свыше 2,5 (25) | Свыше 300 и ниже минус 40 | Вакуум от 0,08 (0,8) (абс) до 2,5 (25) | От минус 40 до 300 | - | - | - | - | - | - |
Вакуум ниже 0,08 (0,8) (абс) | Независимо | - | - | - | - | - | - | - | - |
б) легко- воспламеняющиеся жидкости (ЛВЖ) | Свыше 2,5 (25) | Свыше 300 и ниже минус 40 | Свыше 1,6 (16) до 2,5 (25) | От 120 до 300 | До 1,6 (16) | От минус 40 до 120 | - | - | - | - |
Вакуум ниже 0,08 (0,8) (абс) | Независимо | Вакуум выше 0,08 (0,8) (абс) | От минус 40 до 300 | - | - | - | - | - | - |
в) горючие жидкости (ГЖ) | Свыше 6,3 (63) | Свыше 350 и ниже минус 40 | Свыше 2,5 (25) до 6,3 (63) | Свыше 250 до 350 | Свыше 1,6 (16) до 2,5 (25) | Свыше 120 до 250 | До 1,6 (16) | От минус 40 до 120 | | |
Вакуум ниже 0,003 (0,03) (абс) | То же | Вакуум ниже 0,08 (0,8) (абс) | То же | Вакуум до 0,08 (0,8) (абс) | От минус 40 до 250 | - | - | - | - |
В | Трудногорючие (ТГ) и негорючие вещества (НГ) | Вакуум ниже 0,003 (0,03) (абс) | - | Свыше 6,3 (63) вакуум ниже 0,08 (0,8) (абс) | Свыше 350 до 450 | Свыше 2,5 (25) до 6,3 (63) | От 250 до 350 | Свыше 1,6 (16) до 2,5 (25) | Свыше 120 до 250 | До 1,6 (16) | От минус 40 до 120 |
Приложение 2
к Инструкции по безопасности при эксплуатации
технологических трубопроводов
Выбор типа уплотнительной поверхности фланцев
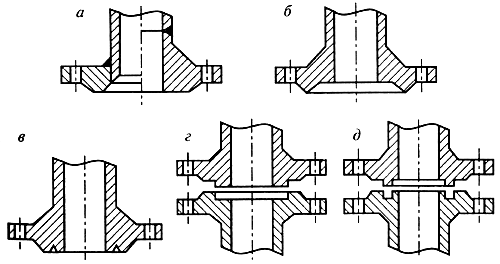
Рис 1. Уплотнительные поверхности фланцев арматуры и соединительных частей трубопроводов:
а - гладкая; б - под линзовую прокладку; в - под кольцевую прокладку овального сечения; г - выступ-впадина; д - шип-паз
Таблица 1
Выбор типа уплотнительной поверхности фланцев
Среда | Давление Pу, Мегапаскаль (килограмм силы на сантиметр квадратный) | Рекомендуемый тип уплотнительной поверхности |
1 | 2 | 3 |
Все вещества группы В | ≤ 2,5 (25) | Гладкая |
Все вещества групп А, Б, кроме А (а) и ВОТ (далее -высокотемпературный органический теплоноситель) | ≥ 2,5 (25) | Гладкая |
Все группы веществ, кроме ВОТ | > 2,5 (25) < 6,3 (63) | Выступ-впадина |
Вещества группы А (а) | ≥ 0,25 (2,5) | Гладкая |
Вещества группы А (а) | > 0,25 (2,5) | Выступ-впадина |
ВОТ | Независимо | Шип-паз |
Фреон, аммиак | Независимо | Выступ-впадина |
Все группы веществ при вакууме | От 0,095 до 0,05 абс. (0,95-0,5) | Гладкая |
Все группы веществ при вакууме | От 0,05 до 0,001 абс. (0,5-0,01) | Шип-паз |
Все группы веществ | ≥ 6,3 (63) | Под линзовую прокладку или прокладку овального сечения |
Приложение 3
к Инструкции по безопасности при эксплуатации
технологических трубопроводов
Ответвления на технологических трубопроводах
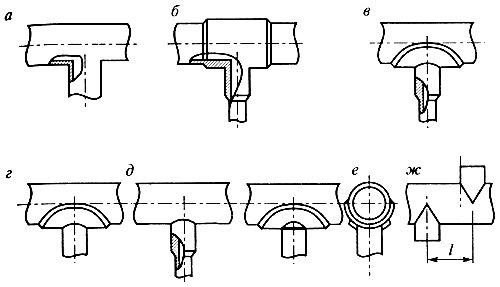
а - без укрепления; б - с помощью тройника; в - укрепленное штуцером и накладкой; г - укрепленное накладкой; д - укрепленное штуцером; е - укрепленное накладками на основной и ответвляемый трубопровод; ж - крестообразное.
Приложение 4
к Инструкции по безопасности при эксплуатации
технологических трубопроводов
Материалы для коррозионных сред
Таблица 1
Максимально допустимая температура применения сталей в водородсодержащих средах, градусов Цельсия
Марка стали | Температура, градусов Цельсия, при парциальном давлении водорода, Мегапаскаль (килограмм силы на сантиметр квадратный) |
1,5(15) | 2,5 (25) | 5 (50) | 10 (100) | 20 (200) | 30 (300) | 40 (400) |
20, 20ЮЧ, 15ГС, 16ГС, 09Г2С, 10Г2 | 290 | 280 | 260 | 230 | 210 | 200 | 190 |
14ХГС | 310 | 300 | 280 | 260 | 250 | 240 | 230 |
30ХМА, 15ХМ, 12Х1МФ, 20Х2МА | 400 | 390 | 370 | 330 | 290 | 260 | 250 |
20Х2МА | 480 | 460 | 450 | 430 | 400 | 390 | 380 |
15Х1М1Ф | 510 | 490 | 460 | 420 | 390 | 380 | 380 |
22X3М | 510 | 500 | 490 | 475 | 440 | 430 | 420 |
18ХЗМФ | 510 | 510 | 510 | 510 | 500 | 470 | 450 |
20Х3МВФ, 15Х5М, 15X5M-III, 08X18H10T, 08Х18Н12Т, 12Х18Н10Т, 12Х18Н12Т, 03Х17Н14М3, 08Х17Н15М3Т, 10Х17Н13М2Т, 10Х17Н13МЗТ | 510 | 510 | 510 | 510 | 510 | 510 | 510 |
Таблица 2
Максимально допустимые парциальные давления окиси углерода, Мегапаскаль (килограмм силы на сантиметр квадратный)
Тип стали | Парциальное давление, Мегапаскаль (килограмм силы на сантиметр квадратный) при температуре, градусов Цельсия |
до 100 | свыше 100 |
Углеродистые и низколегированные с содержанием хрома до 2 процентов | 24 (240) | - |
Низколегированные с содержанием хрома свыше 2 до 5 процентов | - | 10 (100) |
Коррозионно-стойкие стали аустенитного класса | - | 24 (240) |
Таблица 3
Максимально допустимые температуры применения сталей в средах, содержащих аммиак, градусов Цельсия
Марка стали | Температура, градусов Цельсия, при парциальном давлении аммиака, Мегапаскаль (килограмм силы на сантиметр квадратный) |
свыше 1(10) до 2(20) | свыше 2 (20) до 5(50) | свыше 5 (50) до 8(80) |
20, 20ЮЧ, 15ГС, 16ГС, 09Г2С, 10Г2 | 300 | 300 | 300 |
14ХГС, 30ХМА, 15ХМ, 12Х1МФ | 340 | 330 | 310 |
15Х1М1Ф, 20Х2МА, 22Х3М, 18Х3МВ, 15Х5М, 20ХЗМВФ, 15X5M-III | 360 | 350 | 340 |
08X18Н10Т, 08X18Н12Т, 12Х18Н10Т, 12Х18Н12Т, 03Х17Н14М3, 10Х17Н13М2Т, 1РХ17Н13М3Т, 08Х17Н15М3Т | 540 | 540 | 540 |
Приложение 5
к Инструкции по безопасности при эксплуатации
технологических трубопроводов
Условный проход обводной линии не менее, миллиметров:
запорной арматуры | 350-600 | 700-800 | 1000 | 1200 | 1400 |
обводной линии | 50 | 80 | 100 | 125 | 150 |
Приложение 6
к Инструкции по безопасности при эксплуатации
технологических трубопроводов
Расстояние между осями смежных трубопроводов и от трубопроводов до строительных конструкций
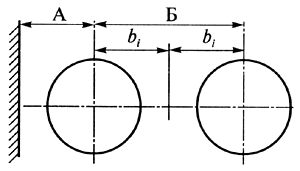
Рекомендуемые расстояния между осями смежных трубопроводов и от трубопроводов до стенок каналов и стен зданий, миллиметров, не менее
Условный проход трубопроводов, Dу, миллиметров | Для изолированных трубопроводов при температуре стенки, градусов Цельсия | Для неизолированных трубопроводов |
без фланцев | с фланцами в одной плоскости при давлении среды, Мегапаскаль (килограмм силы на сантиметр квадратный) |
ниже минус 30 | от минус 30 до 19 | от 20 до 600 | до 1,6 (16) | 2,5 (25) и 4 (40) | 6,3 (63) | 10 (100) |
А | b1 | А | b2 | А | b3 | А | b4 | А | b5 | А | b6 | А | b7 | А | b8 |
10 | 190 | 140 | 170 | 120 | 170 | 120 | 60 | 30 | 100 | 70 | 100 | 70 | 110 | 80 | 110 | 80 |
15 | 190 | 140 | 170 | 120 | 170 | 120 | 60 | 30 | 100 | 70 | 100 | 70 | 110 | 80 | 110 | 80 |
20 | 210 | 160 | 170 | 120 | 200 | 150 | 70 | 40 | 110 | 80 | 110 | 80 | 120 | 90 | 120 | 90 |
25 | 220 | 170 | 180 | 130 | 200 | 150 | 70 | 40 | 110 | 90 | 110 | 90 | 120 | 100 | 120 | 100 |
32 | 240 | 190 | 180 | 130 | 200 | 150 | 70 | 40 | 120 | 100 | 120 | 100 | 130 | 100 | 130 | 100 |
40 | 240 | 190 | 180 | 130 | 200 | 150 | 80 | 50 | 130 | 100 | 130 | 100 | 140 | 110 | 140 | 110 |
50 | 270 | 220 | 210 | 160 | 230 | 180 | 80 | 50 | 130 | 110 | 130 | 110 | 140 | 120 | 150 | 130 |
65 | 300 | 250 | 240 | 190 | 280 | 230 | 90 | 60 | 140 | 120 | 140 | 120 | 150 | 130 | 160 | 140 |
80 | 310 | 260 | 250 | 200 | 310 | 260 | 100 | 70 | 150 | 130 | 150 | 130 | 160 | 130 | 170 | 140 |
100 | 370 | 300 | 310 | 240 | 350 | 280 | 110 | 80 | 160 | 140 | 170 | 140 | 180 | 150 | 190 | 160 |
125 | 410 | 340 | 350 | 280 | 370 | 300 | 120 | 100 | 180 | 150 | 190 | 160 | 200 | 180 | 210 | 180 |
150 | 420 | 350 | 360 | 290 | 380 | 310 | 130 | 110 | 190 | 170 | 200 | 180 | 220 | 200 | 230 | 200 |
175 | 440 | 370 | 380 | 310 | 420 | 350 | 150 | 130 | 210 | 180 | 230 | 200 | 240 | 210 | 250 | 220 |
200 | 450 | 380 | 390 | 320 | 430 | 360 | 160 | 140 | 220 | 190 | 240 | 210 | 260 | 230 | 270 | 240 |
225 | 480 | 410 | 420 | 350 | 440 | 370 | 170 | 150 | 240 | 210 | 260 | 230 | 270 | 240 | 290 | 260 |
250 | 500 | 430 | 440 | 370 | 460 | 390 | 190 | 160 | 260 | 230 | 280 | 250 | 290 | 260 | 330 | 300 |
300 | 560 | 480 | 500 | 420 | 520 | 440 | 210 | 190 | 280 | 260 | 310 | 280 | 320 | 290 | 350 | 320 |
350 | 610 | 530 | 550 | 470 | 550 | 470 | 240 | 210 | 310 | 290 | 340 | 310 | 350 | 330 | 380 | 350 |
400 | 690 | 590 | 630 | 530 | 630 | 530 | 260 | 240 | 340 | 320 | 380 | 360 | 390 | 360 | 410 | 390 |
450 | 740 | 640 | 680 | 580 | 670 | 560 | 290 | 270 | 370 | 350 | 390 | 370 | 450 | 430 | - | - |
500 | 790 | 690 | 730 | 630 | 690 | 590 | 320 | 290 | 410 | 380 | 440 | 410 | 520 | 490 | - | - |
600 | 840 | 740 | 780 | 680 | 760 | 660 | 370 | 340 | 470 | 450 | 500 | 470 | - | - | - | - |
700 | 880 | 780 | 820 | 720 | 800 | 700 | 410 | 380 | 510 | 480 | 550 | 530 | - | - | - | - |
800 | 980 | 860 | 920 | 800 | 860 | 800 | 490 | 450 | 590 | 500 | 650 | 610 | - | - | - | - |
900 | 1030 | 910 | 970 | 850 | 970 | 860 | 540 | 550 | 640 | 600 | - | - | - | - | - | - |
1000 | 1130 | 960 | 1070 | 900 | 1070 | 900 | 610 | 560 | 730 | 680 | - | - | - | - | - | - |
1200 | 1230 | 1060 | 1170 | 1000 | 1170 | 1000 | 710 | 660 | 850 | 800 | - | - | - | - | - | - |
1400 | 1330 | 1160 | 1270 | 1100 | 1270 | 1100 | 810 | 760 | 950 | 900 | - | - | - | - | | - |
| | | | | | | | | | | | | | | | | |
Приложение 7
к Инструкции по безопасности при эксплуатации
технологических трубопроводов
Минимальное расстояние по вертикали от верхних технологических трубопроводов эстакады до линий электропередачи (нижних проводов с учетом их провисания)
Напряжение, Киловольт | до 1 | от 1 до 20 | от 35 до 110 | 150 | 220 |
Расстояние над трубопроводом, метров | 1,0 | 3,0 | 4,0 | 4,5 | 5,0 |
Приложение 8
к Инструкции по безопасности при эксплуатации
технологических трубопроводов
Диаметры
Таблица 1
Диаметр штуцера-кармана в зависимости от диаметра дренируемого трубопровода
Диаметр трубопровода, Dу, миллиметров | от 100 до 125 | от 150 до 175 | от 200 до 250 | от 300 до 350 | от 400 до 450 | от 500 до 600 | от 700 до 800 | от 900 до 1200 |
Диаметр штуцера-кармана, Dу, миллиметров | 50 | 80 | 100 | 150 | 200 | 250 | 300 | 350 |
Таблица 2
Диаметры дренажных штуцеров и запорной арматуры для удаления конденсата из трубопроводов (паропровода) при их продувки паром, в зависимости от диаметра трубопровода
Диаметр трубопровода Dу, миллиметров | до 70 | от 80 до 125 | от 150 до 170 | от 200 до 250 | от 300 до 400 | от 450 до 600 | от 700 до 800 | от 900 до 1200 |
Диаметр штуцера и арматуры Dу, миллиметров | 25 | 32 | 40 | 50 | 80 | 100 | 125 | 150 |
Таблица 3
Диаметры дренажных штуцеров
Диаметр трубопровода Dу, миллиметров | от 25 до 80 | от 100 до 150 | от 175 до 300 | от 350 до 450 | от 500 до 700 | от 800 до 1200 |
Диаметр штуцера Dу, миллиметров | 15 | 20 | 25 | 32 | 40 | 50 |
Приложение 9
к Инструкции по безопасности при эксплуатации
технологических трубопроводов
Допустимое смещение внутренних кромок при сборке стыков труб
Условное давление Ру, Мегапаскаль (килограмм силы на сантиметр квадратный) | Категория трубопроводов | Величина смещения в зависимости от номинальной толщины стенки S, миллиметров |
кольцевой шов | продольный шов |
Свыше 10 (100) до 320 (3200) и I категории при температуре ниже минус 70 градусов Цельсия | | 0,10 S, но не более 1 миллиметра | |
До 10 (100) | I и II | 0,15 S, но не более 2 миллиметров | 0,10 S, но не более 1 миллиметра |
III и IV | 0,20 S, но не более 3 миллиметров | 0,15 S, но не более 2 миллиметров |
V | 0,30 S, но не более 3 миллиметров | 0,20 S, но не более 3 миллиметров |
Приложение 10
к Инструкции по безопасности при эксплуатации
технологических трубопроводов
Оценка качества сварных соединений трубопроводов по результатам радиографического контроля в зависимости от размеров объемных дефектов (включений, пор)
Оценка в баллах | Толщина стенки, миллиметров | Включения (поры) | Скопления, длина, миллиметров | Суммарная длина на любом участке шва длиной 100 миллиметров |
ширина (диаметр), миллиметров | длина, миллиметров |
1 | До 3 | 0,5 | 1,0 | 2,0 | 3,0 |
Свыше 3 до 5 | 0,6 | 1,2 | 2,5 | 4,0 |
Свыше 5 до 8 | 0,8 | 1,5 | 3,0 | 5,0 |
Свыше 8 до 11 | 1,0 | 2,0 | 4,0 | 6,0 |
Свыше 11 до 14 | 1,2 | 2,5 | 5,0 | 8,0 |
Свыше 14 до 20 | 1,5 | 3,0 | 6,0 | 10,0 |
Свыше 20 до 26 | 2,0 | 4,0 | 8,0 | 12,0 |
Свыше 26 до 34 | 2,5 | 5,0 | 10,0 | 15,0 |
Свыше 34 | 3,0 | 6,0 | 10,0 | 20,0 |
2 | До 3 | 0,6 | 2,0 | 3,0 | 6,0 |
Свыше 3 до 5 | 0,8 | 2,5 | 4,0 | 8,0 |
Свыше 5 до 8 | 1,0 | 3,0 | 5,0 | 10,0 |
Свыше 8 до 11 | 1,2 | 3,5 | 6,0 | 12,0 |
Свыше 11 до 14 | 1,5 | 5,0 | 8,0 | 15,0 |
Свыше 14 до 20 | 2,0 | 6,0 | 10,0 | 20,0 |
Свыше 20 до 26 | 2,5 | 8,0 | 12,0 | 25,0 |
Свыше 26 до 34 | 2,5 | 8,0 | 12,0 | 30,0 |
Свыше 34 до 45 | 3,0 | 10,0 | 15,0 | 30,0 |
Свыше 45 | 3,5 | 12,0 | 15,0 | 40,0 |
3 | До 3 | 0,8 | 3,0 | 5,0 | 8,0 |
Свыше 3 до 5 | 1,0 | 4,0 | 6,0 | 10,0 |
Свыше 5 до 8 | 1,2 | 5,0 | 7,0 | 12,0 |
Свыше 8 до 11 | 1,5 | 6,0 | 9,0 | 15,0 |
Свыше 11 до 14 | 2,0 | 8,0 | 12,0 | 20,0 |
Свыше 14 до 20 | 2,5 | 10,0 | 15,0 | 25,0 |
Свыше 20 до 26 | 3,0 | 12,0 | 20,0 | 30,0 |
Свыше 26 до 34 | 3,5 | 12,0 | 20,0 | 35,0 |
Свыше 34 до 45 | 4,0 | 15,0 | 25,0 | 40,0 |
Свыше 45 | 4,5 | 15,0 | 30,0 | 45,0 |
4 | Независимо от толщины | Включения (поры), скопления, размер или суммарная протяженность которых превышают установленные для балла 3 настоящей таблицы |
Приложение 11
к Инструкции по безопасности при эксплуатации
технологических трубопроводов
Объем контроля сварных соединений ультразвуковым или радиографическим методом в процентах от общего числа сваренных каждым сварщиком (но не менее одного) соединений
Условия изготовления стыков | Категория трубопроводов |
Ру>10 Мегапаскаль (килограмм силы на сантиметр квадратный) и I категории при температуре ниже минус 70 градусов Цельсия | 1 | 2 | 3 | 4 | 5 |
При изготовлении и монтаже в организации нового трубопровода, а также при ремонте | 100 | 20 | 10 | 2 | 1 | Согласно условиям пункта 271 к настоящей Инструкции |
При сварке разнородных сталей | 100 | 100 | 100 | 100 | 100 | 10 |
При сварке трубопроводов, входящих в блоки I категории взрывоопасности | 100 | 100 | 10 | 2 | 1 | - |
Приложение 12
к Инструкции по безопасности при эксплуатации
технологических трубопроводов
Оценка качества сварных соединений трубопроводов по результатам радиографического контроля в зависимости от величины и протяженности плоских дефектов (непровары по оси шва, несплавления)
Оценка в баллах | Непровары по оси шва, несплавления, трещины, вогнутость и выпуклость металла в корне шва |
Глубина, процентов к номинальной толщине стенки | Допустимая суммарная длина по периметру трубы |
0 | Непровар отсутствует | |
Вогнутость корня шва до 10 процентов, но не более 1,5 миллиметра | До 1/8 периметра |
Выпуклость корневого шва до 10 процентов, но не более 3 миллиметров | До 1/8 периметра |
1 | Непровар по оси шва до 10 процентов, но не более 2 миллиметров | До 1/4 периметра |
или до 5 процентов, но не более 1 миллиметра | До 1/2 периметра |
2 | Непровар по оси шва до 20 процентов, но не более 3 миллиметров | До 1/4 периметра |
или до 10 процентов, но не более 2 миллиметров | До 1/2 периметра |
или до 5 процентов, но не более 1 миллиметра | Не ограничивается |
6 | Непровары по оси шва более 20 процентов и более 3 миллиметров | Независимо от длины |
Трещины любой глубины | Независимо от длины |
Несплавления между основным металлом и швом и между отдельными валиками шва | Независимо от длины |
Сварные соединения признаются негодными, если суммарный балл равен или больше значений, указанных ниже:
Категория трубопровода | Давление Ру> 10 Мегапаскаль (килограмм силы на сантиметр квадратный) | 1 категории, при температуре ниже минус 70 градусов Цельсия | 1 | 2 | 3 | 4 | 5 |
Суммарный балл | 2 | 2 | 3 | 3 | 5 | 6 | 6 |
Приложение 13
к Инструкции по безопасности при эксплуатации
технологических трубопроводов
Значения допустимых дефектов в сварных швах трубопроводов Pу≤10 Мегапаскаль (100 килограмм сила на сантиметр квадратный), выявленных при ультразвуковом контроле
Номинальная толщина стенки Н, миллиметров | Эквивалентная площадь (размеры) отдельных дефектов | Условная протяженность цепочки точечных дефектов на участке сварного шва длиной 10Н |
Наименьшая фиксируемая, дециБелл | По отверстию с плоским дном, миллиметров в квадрате | По зарубке, миллиметров×миллиметров |
8-10 | На 6 дециБелл ниже эхо-сигнала от максимально допустимых эквивалентных дефектов | 1,6 | 1,0×2,0 | 1,5Н |
12-18 | 2,0 | 2,0×2,0 | 1,5Н |
20-24 | 3,0 | 3,0×2,0 | 1,5Н |
Приложение 14
к Инструкции по безопасности при эксплуатации
технологических трубопроводов
Оценка качества сварных соединений по твердости
Марка стали | Допустимая твердость металла шва и зоны термического влияния, НВ, не более |
14ХГС | 230 |
15ХМ, 12Х1МФ, 15Х1М1Ф, 15Х2М1, 15Х5М, 15Х5МУ, 15Х5ВФ | 240 |
30ХМА, 20Х2МА, 22Х3М, 18Х3МВ | 270 |
20Х3МВФ | 300 |
Приложение 15
к Инструкции по безопасности при эксплуатации
технологических трубопроводов
Допустимые размеры выборки после удаления дефектов в сварных швах трубопроводов
Глубина выборки, процентов от номинальной толщины стенки труб или расчетного сечения шва | Суммарная протяженность выборки, процентов от номинального наружного периметра сварного соединения |
Для трубопроводов давлением Ру свыше 10 Мегапаскаль (килограмм силы на сантиметр квадратный), трубопроводов I категории, работающих при температуре ниже минус 70 градусов Цельсия |
15 и менее | Не нормируется |
Более 15 до 30 включительно | до 35 |
Более 30 до 50 включительно | до 20 |
Более 50 | до 15 |
Для трубопроводов I - IV категории |
25 и менее | Не нормируется |
Более 25 до 50 включительно | до 50 |
Более 50 | до 25 |
Для трубопровода V категории |
30 и менее | Не нормируется |
Более 30 до 50 включительно | до 50 |
Более 50 | до 35 |
Приложение 16
к Инструкции по безопасности при эксплуатации
технологических трубопроводов
Количество контрольных сварных соединений для проведения механических испытаний и металлографических исследований
Условный диаметр трубы Dу, миллиметров | Количество контрольных соединений |
6-32 | 4 |
50-150 | 2 |
175 и выше | 1 |