В2 - вертикальное (сварка сверху вниз);
П1 - потолочное;
П2 - потолочное тавровых соединений.
Рисунок 2. Положения при сварке стыковых (а) и угловых (б) соединений труб
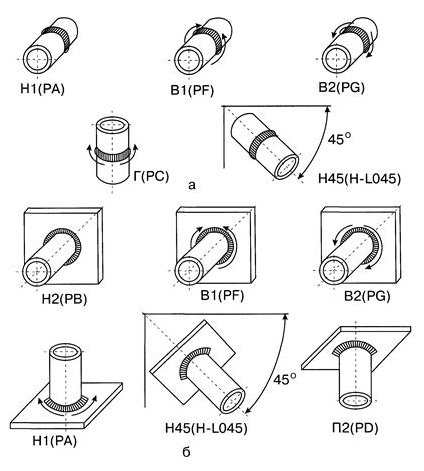
Примечания:
Н1 - нижнее при горизонтальном расположении осей труб, свариваемых с поворотом;
Н2 - нижнее при вертикальном расположении оси трубы, свариваемой без поворота или с поворотом и горизонтальном расположении оси трубы, привариваемой с поворотом;
В1 - переменное при горизонтальном расположении осей труб (трубы) свариваемых без поворота (на подъем);
В2 - переменное при горизонтальном расположении осей труб (трубы) свариваемых без поворота (на спуск);
Г - горизонтальное при вертикальном расположении осей труб, свариваемых без поворота или с поворотом;
Н45 - переменное при наклонном расположении осей труб (трубы) свариваемых без поворота;
П2 - потолочное при вертикальном расположении оси трубы, свариваемой без поворота или с поворотом.
Рисунок 3. Размеры деталей для стыковых контрольных сварных соединений листов
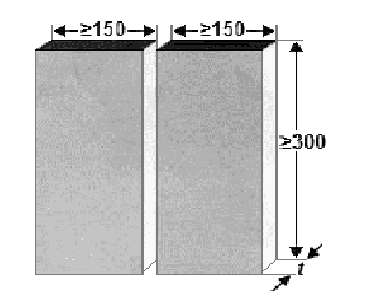
Рисунок 4. Размеры деталей для тавровых контрольных сварных соединений листов
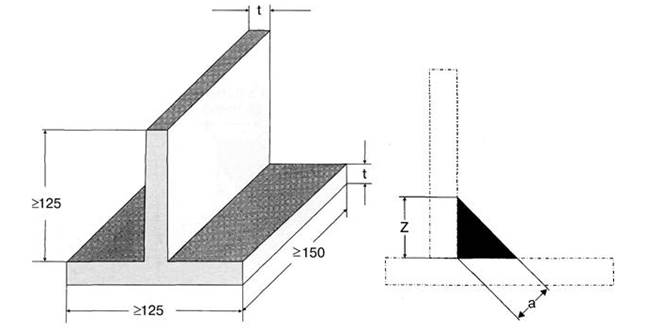
Примечания:
При t ≥ 6 мм, а ≤ 0,5t;
При t 6 мм, 0,5t ≤ а ≤ (Z = 0,7t).
Рисунок 5. Размеры деталей для стыковых контрольных сварных соединений металлических труб
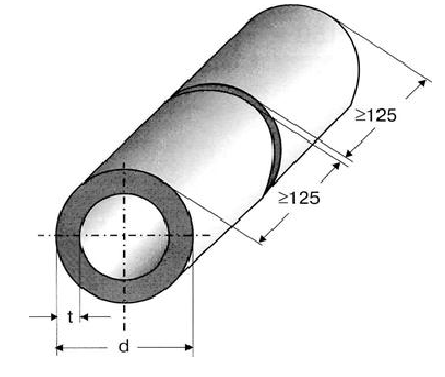
Рисунок 6. Размеры деталей для угловых контрольных сварных соединений труб между собой и труб с листами
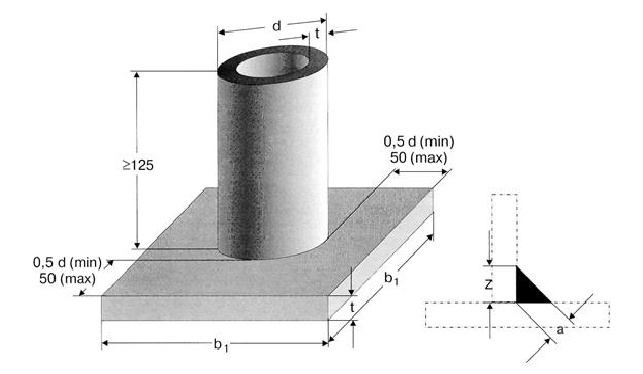
Примечания:
При t ≥ 6 мм, а ≤ 0,5t;
При t 6 мм, 0,5t ≤ а ≤ (Z = 0,7t).
Рисунок 7. Типы контрольных сварных соединений при сварке труб из полимерных материалов
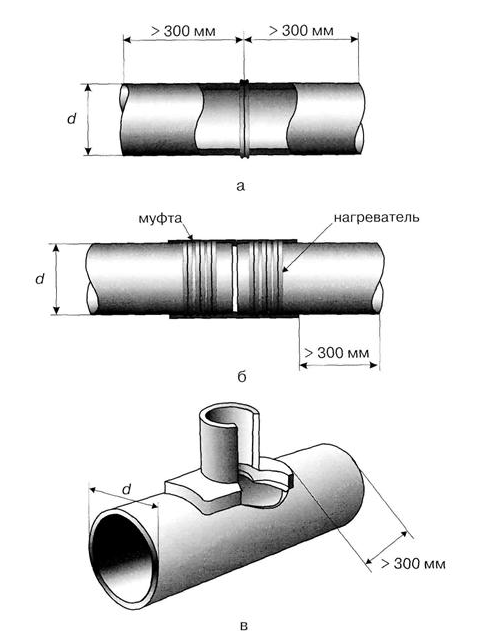
Примечания:
а - стыковое соединение;
б - соединение муфтой;
в - соединение седловым ответвлением.
Рисунок 8. Контрольное сварное соединение типа Р
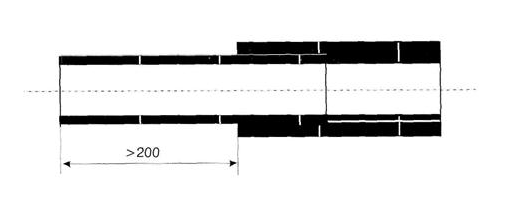
Рисунок 9. Контрольные сварные соединения типов V и Х
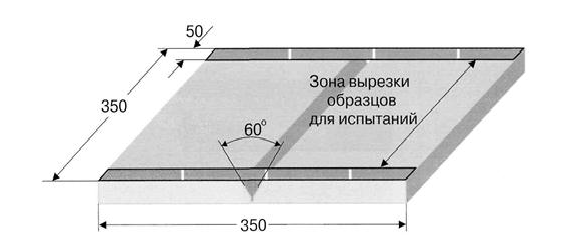
Рисунок 10. Контрольные сварные соединения типов ТБ, ТV и TX
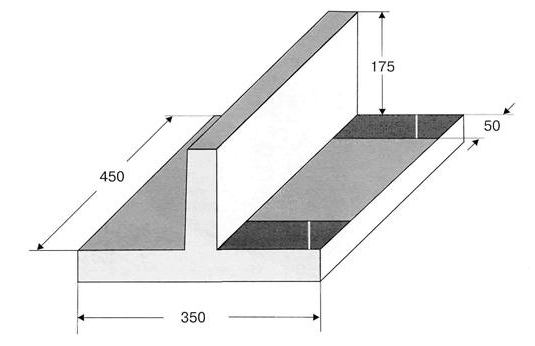
Рисунок 11. Контрольное сварное соединение типа Н
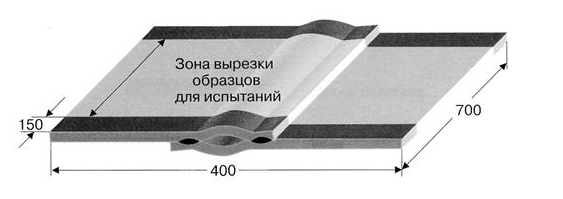
Приложение 6
к Правилам аттестации
сварщиков и специалистов
сварочного производства
Форма
Карта технологического процесса сварки (наплавки) контрольного сварного соединения
УТВЕРЖДАЮ
Руководитель аттестующей организации
(подпись) (Ф.И.О. (при наличии)
«___» ____________________ 20__ г.
Ф.И.О. (при наличии) сварщика | | Клеймо | |
Вид и способ сварки или наплавки | | Основной материал (марка) | |
Наименование НД (шифр) | | | |
| | | |
Вид шва | | Типоразмер, мм: | |
Тип соединения (по НД) | | диаметр | |
| | толщина | |
| | | |
Положение при сварке | | Способ сборки | |
Вид соединения | | Требования к прихватке | |
Присадочные материалы (марка, стандарт, ТУ) | | | |
| | Сварочное оборудование | |
Эскиз контрольного сварного соединения
Конструкция соединения | Размеры шва | Порядок сварки |
| | |
Технологические параметры сварки
Номер шва или валика | Вид и способ сварки | Диаметр электрода или проволоки, мм | Род и полярность тока | Сила тока, А | Напряжение, В | Скорость подачи проволоки, м/ч | Скорость сварки, м/ч | Расход защитного газа, л/мин |
| | | | | | | | |
Защита обратной стороны шва | | Вылет электрода, мм | |
Ширина шва или валика (катет шва), мм | | Расстояние от сопла горелки до изделия, мм | |
Толщина шва или валика, мм | |
| | | | | | | | | | |
Дополнительные технологические требования по сварке
_________________________________________________________________________
_________________________________________________________________________
Требования к контролю качества контрольных сварных соединений
Метод контроля | Наименование (шифр) | Объем контроля (%, количество образцов) |
1. Визуально-измерительный | | | |
2. Радиографический | | | |
3. Ультразвуковой | | | |
4. Капиллярный | | | |
5. Магнитопорошковый | | | |
6. Анализ макрошлифов | | | |
7. Испытания на статический изгиб (сплющивание) | | | |
8. Испытания на излом | | | |
Разработал (подпись, дата) | Ф.И.О. (при наличии) |
Приложение 7
к Правилам аттестации
сварщиков и специалистов
сварочного производства
Форма
Карта технологического процесса сварки полимерных труб встык нагретым инструментом
Наименование изделия | контрольное | Характеристика труб (деталей) | |
Сварное соединение | | - завод изготовитель | |
Способ сварки | НИ | - марка материала | полиэтилен ПЭ80 |
Документы по сварке | МСП 4.03-103 «Проектирование, строительство и реконструкция газопроводов с применением полиэтиленовых труб»; СП 42-105 «Контроль качества сварных соединений полиэтиленовых газопроводов» | - дата выпуска | |
- номер сертификата | |
- диаметр трубы | 110 мм |
Вид соединения | стыковое | - толщина стенки, SDR | 10 мм |
Сварочное оборудование | СР | | |
Ф.И.О. (при наличии) сварщика | | Клеймо сварщика | |
Эскиз сварного соединения
Конструкция сборки | Конструктивные элементы сварного соединения |
| |
Технологические параметры сварки труб встык нагревательным инструментом и их значения (в соответствии с МСП 4.03-103 «Проектирование, строительство и реконструкция газопроводов с применением полиэтиленовых труб»)
Технологический параметр | Значение |
1. Температура нагревателя (Тн), оС - теплогенератор электрический с непрерывным автоматическим поддержанием заданной температуры, с антиадгезионным покрытием | 220 |
2. Удельное давление при оплавлении (Ропл), МПа | 0,15+0,05 |
3. Время при оплавлении (tопл), с, в зависимости от типа свариваемых труб | до 15 (до образования первичного грата высотой 1 мм) |
4. Давление при прогреве (Рпр), МПа | 0,01-0,02 |
5. Время при прогреве (tпр), с, в зависимости от типа свариваемых труб и температуры окружающего воздуха | Температура окружающего воздуха, оС |
от 0 до +20 | от 0 до +20 |
70-80 | 65-75 |
6. Время технологической паузы (tп), с, не более | 4 |
7. Удельное давление при осадке (Рос), МПа | 0,15+0,05 |
8. Время при охлаждении (tохл), мин, не менее, в зависимости от температуры окружающего воздуха | Температура окружающего воздуха, оС |
от 0 до + 20 | от +20 до +40 |
7 | 8 |
Примечания:
Значения параметров корректируются в зависимости от температуры окружающего воздуха.
Дополнительные технологические требования по сварке:
очистить поверхности концов свариваемых труб сначала увлажненной, затем сухой ветошью на длину не менее 50 мм от торцов;
установить и закрепить трубы в зажимах центратора установки для сварки;
отцентрировать трубы по наружной поверхности таким образом, чтобы максимальная величина смещения наружных кромок не превышала 10 % от номинальной толщины стенки свариваемых труб;
отторцевать свариваемые поверхности труб непосредственно в сварочной установке;
еще раз проверить центровку труб и отсутствие недопустимых зазоров в стыке (допускается зазор в стыке не более 0,3 мм). Зазоры измеряют лепестковым щупом с погрешностью 0,05 мм;
произвести замер усилия при холостом ходе подвижного зажима центратора установки с закрепленной в нем трубой и скорректировать величину усилий Ропл, Рпр, Рос;
установить требуемые параметры режима сварки и произвести сварку контрольного соединения;
после сварки произвести охлаждение стыка под давлением осадки в течение времени tохл;
проставить клеймо сварщика маркером на наружной поверхности трубы;
удалить контрольное сварное соединение из установки для сварки и провести визуальный и измерительный контроль сварного соединения.
Требования к контролю качества
Метод контроля | Наименование (шифр) документа по сварке | Объем контроля (%, количество образцов) |
1. Визуальный и измерительный | МСП 4.03-103 «Проектирование, строительство и реконструкция газопроводов с применением полиэтиленовых труб»; СП 42-105 «Контроль качества сварных соединений полиэтиленовых газопроводов» | 100 % |
2. Ультразвуковой | Инструкция по ультразвуковому контролю сварных стыковых соединений полиэтиленовых труб | 100 % |
3. Испытание на статическое растяжение | ГОСТ 11262 «Пластмассы. Методы испытания на растяжение»; СП 42-105 «Контроль качества сварных соединений полиэтиленовых газопроводов» | ≥ 5 образцов |
Разработал (подпись, дата) | Ф.И.О. (при наличии) |
Приложение 8
к Правилам аттестации
сварщиков и специалистов
сварочного производства
Форма
Карта технологического процесса сварки полимерных труб с применением деталей с закладными нагревателями
Наименование изделия | контрольное | Характеристика труб (деталей) | |
Сварное соединение | | - завод изготовитель | |
Способ сварки | ЗН | - марка материала | |
Документы по сварке | МСП 4.03-103 «Проектирование, строительство и реконструкция газопроводов с применением полиэтиленовых труб»; СП 42-105 «Контроль качества сварных соединений полиэтиленовых газопроводов» | - дата выпуска | |
- номер сертификата | |
- диаметр трубы | 50 мм |
Вид соединения | стыковое | - толщина стенки, SDR | 4,5 мм |
Сварочное оборудование | ЗНШ | | |
Ф.И.О. (при наличии) сварщика | | Клеймо сварщика | |
Технологические параметры сварки |
Температура окружающего воздуха, 0С | Наружный диаметр трубы, мм | Толщина стенки, мм | SDR | Время охлаждения после сварки, мин |
20 | 50 | 4,5 | 11 | 7 |
Примечания:
При сварке на аппаратах с ручным вводом параметров режима сварки указывают их действительные значения.
Дополнительные технологические требования по сварке:
обрезать трубы, предназначенные для сварки под прямым углом к их осям;
отметить на концах трубы зону сварки на длину не менее 0.5 длины фитинга от торцов;
произвести механическую очистку поверхностей труб в зоне сварки от оксидного слоя на глубину 0,1-0,2 мм;
снять фаски на наружной и внутренней поверхностях торца трубы;
придать трубе в зоне сварки круглую форму с помощью приспособления;
произвести обезжиривание зоны сварки;
нанести маркировочные полосы на поверхность труб на расстоянии 0,5 длины фитинга от торца трубы;
зафиксировать положение труб в позиционере или на выравнивающих опорах;
вставить концы труб в фитинг и подключить его к сварочному аппарату;
ввести с помощью считывающего карандаша в сварочный аппарат параметры режима сварки, указанные в штрих-коде на этикетке фитинга;
включить сварочный аппарат и произвести сварку;
провести визуальный и измерительный контроль сварного соединения.
Требования к контролю качества
Метод контроля | Наименование (шифр) документа по сварке | Объем контроля (%, количество образцов) |
1. Визуальный и измерительный | МСП 4.03-103 «Проектирование, строительство и реконструкция газопроводов с применением полиэтиленовых труб»; СП 42-105 «Контроль качества сварных соединений полиэтиленовых газопроводов» | 100 % |
2. Испытания на сплющивание | МСП 4.03-103 «Проектирование, строительство и реконструкция газопроводов с применением полиэтиленовых труб»; СП 42-105 «Контроль качества сварных соединений полиэтиленовых газопроводов» | ≥ 2 образцов |
Разработал (подпись, дата) | Ф.И.О. (при наличии) |
Приложение 9
к Правилам аттестации сварщиков
и специалистов сварочного
производства
Форма
Журнал учета работ при аттестации сварщиков металлических конструкций (практический экзамен)
№, дата | Ф.И.О. (при наличии) | Номер заявки, вид аттестации | Наименование (шифр) технологии сварки (наплавки), способ сварки | Характеристика контрольного сварного соединения | Клеймо контрольного сварного соединения |
Марка основного материала | Марки сварочных материалов | Вид свариваемых деталей и типоразмер, мм | Тип шва | Тип соединения | Вид соединения | Положение шва при сварке |
1 | 2 | 3 | 4 | 5 | 6 | 7 | 8 | 9 | 10 | 11 | 12 |
Продолжение таблицы
Отметка о выдаче задания | Отметка о контроле качества сборки соединения под сварку | Отметка о соблюдении технологии сварки | Продолжительность сварки контрольного соединения | Методы контроля и оценка качества | Заключение комиссии |
Подпись лица, выдавшего задание, дата | Подпись аттестуемого сварщика, дата |
13 | 14 | 15 | 16 | 17 | 18 | 19 |
Примечания:
В графе 4 указывают наименование и номер карты технологического процесса сварки (наплавки) контрольного сварного соединения.
Заполнение граф 7-11 производят условными обозначениями, установленными настоящими Правилами.
В графе 12 указывают номер клейма установленного аттестационной комиссией. Клеймение выполняют ударным или электрографическим способами.
Графы 13, 15, 16 и 17 заполняет член аттестационной комиссии.
В графе 16 указывают сведения о прерываниях процесса сварки, подогрева, поддува защитного газа, контроле температуры металла при сварке, зачистке корня шва и другие.
В графе 18 указывают метод контроля, номер акта (протокола, заключения) и результаты контроля (удовлетворительно, неудовлетворительно). При заполнении графы допускается сокращенное обозначение применяемых методов неразрушающего контроля - радиографический - РГК, ультразвуковой - УЗК, капиллярный - КК, магнитопорошковый - МПК, визуальный и измерительный - ВИК.
В графе 19 аттестационная комиссия указывает оценку практических навыков сварщика словами «удовлетворительно» или «неудовлетворительно». Заключение подписывают члены аттестационной комиссии с указанием даты.
Страницы журнала пронумеровываются и прошнуровываются.
Приложение 10
к Правилам аттестации
сварщиков и специалистов
сварочного производства
Форма
Журнал учета работ при аттестации сварщиков (практический экзамен, сварка полимерных материалов)
№ дата | Ф. И.О. | Номер заявки, вид аттестации | Наименование (шифр) технологии сварки, способ сварки | Характеристика контрольного сварного соединения |
Марки материалов свариваемых деталей | Марки сварочных материалов или деталей | Вид свариваемых деталей и типоразмер, мм | Тип сварного соединения | Степень автоматизации оборудования, номер распечатки | | |
1 | 2 | 3 | 4 | 5 | 6 | 7 | 8 | 9 | | |
Продолжение таблицы
Клеймо контрольного сварного соединения | Отметка о выдаче задания | Отметка о соблюдении технологии | Результаты ВИК | Результаты мех. испытаний | Результаты УЗК | Заключение комиссии |
Подпись лица, выдавшего задание, дата | Подпись аттестуемого сварщика, дата |
10 | 11 | 12 | 13 | 14 | 15 | 16 | 17 |
Примечания:
В графе 4 указывают номер «Технологического регламента процесса сварки контрольного сварного соединения».
Заполнение граф 7-9 производят условными обозначениями, установленными настоящими Правилами.
Тип сварного соединения (графа 8) указывают буквами в соответствии с приложением 4 (таблица 5) к настоящим Правилам.
Степень автоматизации сварочного оборудования (графа 9) указывают условным обозначением в соответствии с пунктом 38 настоящих Правил.
В графе 10 указывают номер клейма, установленного экзаменационной комиссией.
Графы 13-17 заполняет член экзаменационной комиссии.
В графе 17 экзаменационная комиссия указывает оценку практических навыков сварщика словами «удовлетворительно» или «неудовлетворительно». Заключение подписывают члены экзаменационной комиссии с указанием даты и места проведения практического экзамена.
Страницы журнала пронумеровываются и прошнуровываются.
Приложение 11
к Правилам аттестации сварщиков
и специалистов сварочного
производства
Визуальный и измерительный контроль стыковых контрольных сварных соединений из полимерных материалов
1. Визуальный контроль стыковых контрольных сварных соединений производит член экзаменационной комиссии по всей протяженности шва с двух сторон с использованием лупы увеличением 5-7 крат. Измерительный контроль выполняют не менее чем в 5 местах сварного соединения, расположенных равномерно. Выбор мест измерения выполняет представитель экзаменационной комиссии.
2. Внешний вид сварных соединений, выполненных сваркой нагретым инструментом встык, соответствуют следующим требованиям:
валики сварного шва симметрично и равномерно распределены по окружности сваренных труб;
цвет валиков одного цвета с трубой и без трещин, пор, инородных включений;
симметричность шва (отношение ширины наружных валиков грата к общей ширине грата) в пределах 0,3-0,7 в любой точке шва;
смещение наружных кромок свариваемых заготовок не превышает 10 % от толщины стенки трубы (детали);
впадина между валиками грата (линия сплавления наружных поверхностей валиков грата) находится не ниже наружной поверхности труб (деталей);
угол излома сваренных труб или трубы и соединительной детали не превышает 5 градусов.
3. Размеры валиков наружного грата швов зависят от толщины стенки свариваемых труб (деталей) и соответствуют следующим данным:
Геометрические размеры сварного шва
Параметры наружного грата | Условное обозначение труб |
SDR11 63х5,8 | SDR11 75х6,8 | SDR7,6 90х5,2 | SDR11 90х8,2 | SDR17,6 110x6,3 | SDR11 110х10 |
Высота, мм | 1,5-3,0 | 2,0-3,5 | 1,5-3,0 | 2,5-4,5 | 2,0-3,5 | 2,5-4,5 |
Ширина, мм | 4,0-6,0 | 5,0-7,0 | 4,0-6,0 | 6,0-8,5 | 4,5-6,5 | 6,5-9,5 |
Параметры наружного грата | Условное обозначение труб |
SDR17,6 125х7,1 | SDR11 125х11,4 | SDR17,6 140х8,0 | SDR11 140х12,7 | SDR17,6 160х9,1 | SDR11 160х14,6 |
Высота, мм | 2,0-4,0 | 3,0-5,0 | 2,5-4,5 | 3,0-5,0 | 2,5-4,5 | 3,0-5,0 |
Ширина, мм | 5,5-7,5 | 8,5-12,0 | 6,0-8,5 | 9,0-13,0 | 6,5-9,5 | 10-15 |
Параметры наружного грата | Условное обозначение труб |
SDR17,6 180х10,2 | SDR11 180х16,4 | SDR17,6 200х11,4 | SDR11 200х18,2 | SDR17,6 225х12,8 | SDR11 225х20,5 |
Высота, мм | 2,5-4,5 | 3,5-5,5 | 3,0-5,0 | 4,0-6,0 | 3,0-5,0 | 4,5-6,5 |
Ширина, мм | 6,5-9,5 | 11-16 | 8,5-12 | 13-18 | 9,0-13,0 | 14-21 |
Приложение 12
к Правилам аттестации сварщиков
и специалистов сварочного
производства
Визуальный и измерительный контроль контрольных сварных соединений из полимерных материалов, выполненных сваркой с закладными нагревательными элементами
1. Визуальный и измерительный контроль контрольных сварных соединений производит член экзаменационной комиссии с использованием лупы увеличением 5-7 крат. Выбор мест измерения выполняет представитель экзаменационной комиссии.
2. Внешний вид контрольных сварных соединений, выполненных при помощи деталей с закладными нагревательными элементами, соответствуют следующим требованиям:
трубы за пределами соединительной детали имеют следы механической обработки (зачистки);
индикаторы сварки деталей находятся в выдвинутом положении;
угол излома сваренных труб или трубы и соединительной детали не превышает 5 градусов;
поверхность деталей не имеет следов температурной деформации или сгоревшего полимерного материала;
по периметру детали не допускается следов расплава полимерного материала, возникшего в процессе сварки.
Приложение 13
к Правилам аттестации сварщиков
и специалистов сварочного
производства
Испытания контрольных сварных соединений на статический изгиб
1. Механические испытания контрольных сварных соединений металлических материалов проводят в соответствии с ГОСТ 6996 «Сварные соединения. Методы определения механических свойств» (далее - ГОСТ 6996), полимерных материалов - в соответствии с ГОСТ 11262 «Пластмассы. Методы испытания на растяжение».
2. Испытаниям на статический изгиб стыковых соединений листов и труб толщиной 3 мм и более подлежат 4 образца, из которых 2 образца подлежат изгибу со стороны усиления шва, а другие 2 образца - со стороны корня шва. При толщине листов и стенок труб 12 мм и более допускается выполнять испытание образцов «на ребро» (боковой изгиб). При этом испытаниям подлежат не менее 4 образцов.
3. Для стыковых соединений металлических труб диаметром до 108 мм включительно при толщине стенки до 6 мм включительно допускается проводить испытания на сплющивание, если это не противоречит требованиям национальных и (или) межгосударственных стандартов.
4. Вырезку заготовок для изготовления образцов для механических испытаний производят механическим путем режущим или абразивным инструментом. Допускается вырезку заготовок выполнять плазменной или газовой резкой при условии последующей механической обработки заготовок в зоне резки на глубину не менее 2 мм. Краевые участки стыкового и таврового контрольных сварных соединений пластин, выполненных ручными способами сварки, длиной не менее 25 мм подлежат удалению.
При автоматической и механизированной сварке в среде защитных газов и порошковой проволокой при толщине металла более 10 мм, автоматической сварке под флюсом, электрошлаковой сварке длину краевых участков принимать в соответствии с указаниями ГОСТ 6996.
5. При изготовлении образцов усиление шва с наружной и внутренней стороны следует удалять механическим путем. Перед изготовлением образцов остающаяся стальная подкладка в контрольных сварных соединениях, выполненных с подкладкой, удаляется.
Рисунок 1. Схемы испытаний на статический изгиб со стороны усиления шва (а), со стороны корня шва (б) и на боковой изгиб - изгиб «на ребро» (в) образцов из контрольных стыковых сварных соединений листов и труб
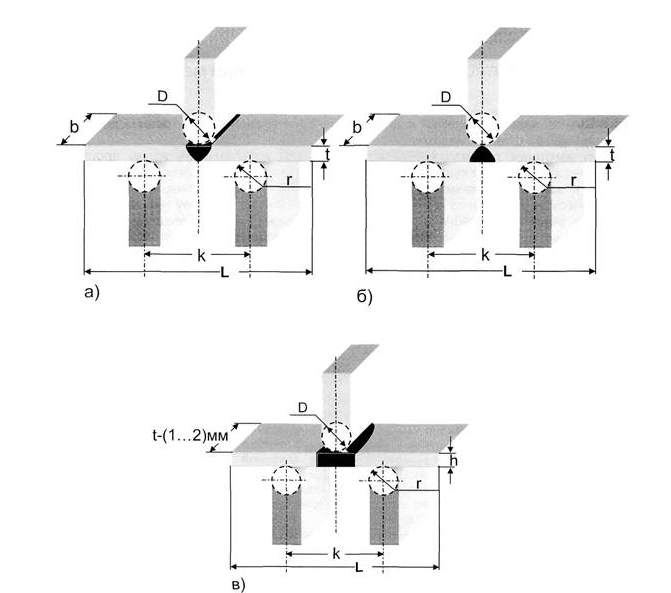
Примечание:
Рекомендуемые параметры: D - диаметр пуансона, L - длина образца; b = 1,5t, но не менее 10 мм; D = 2t или D = 2h; r = t, но не более 25 мм; K = 2,5D; L = D + 2,5h + 80мм.
Приложение 14
к Правилам аттестации сварщиков
и специалистов сварочного
производства
Испытания контрольных сварных соединений металлических изделий на излом
1. Испытания на излом выполняют с целью выявления возможных внутренних дефектов в сечении шва в месте его излома.
2. Вырезку заготовок для изготовления образцов для испытаний на излом производят механическим путем режущим или абразивным инструментом. Допускается выполнять вырезку заготовок плазменной или газовой резкой при условии последующей механической обработки заготовок в зоне резки на глубину не менее 2 мм. Краевые участки стыкового и таврового контрольных сварных соединений пластин, выполненных ручными способами сварки, длиной не менее 25 мм подлежат удалению.
Заготовки образцов для испытаний на излом, имеющие надрез по боковым поверхностям глубиной 5 мм, допускается не обрабатывать механическим путем после плазменной и газовой резки.
3. Усиление шва допускается не удалять. Перед изготовлением образцов остающаяся стальная подкладка в контрольных сварных соединениях, выполненных с подкладкой, удаляется.
4. Испытаниям подвергается вся длина стыкового и углового контрольных сварных соединений листов (без краевых участков длиной 25 мм, удаляемых при вырезке заготовок) и труб.
5. Из контрольного стыкового соединения листов вырезают образцы для испытаний шириной 50 мм. При необходимости допускается удалять усиление шва. В образцах на обоих концах сварного шва делаются надрезы глубиной до 5 мм и шириной 2 мм для улучшения условий разрушения наплавленного металла.
6. На образцах допускается выполнять надрез глубиной до 1 мм со стороны, противоположной месту приложения изгибающей нагрузки.
7. При односторонней сварке соединения без подкладки, половину всех образцов следует изгибать, прикладывая нагрузку со стороны корня шва, а другую половину - со стороны усиления.
8. При испытании на излом угловых контрольных сварных соединений листов контрольный образец после удаления краевых частей испытывают либо целиком, либо разрезают на несколько отдельных контрольных образцов шириной не менее 40 мм.
9. При испытании на излом стыкового контрольного сварного соединения труб из него вырезают образцы для испытаний шириной 50 мм. При этом количество образцов для испытаний - не менее 4. Если диаметр трубы контрольного соединения не позволяет вырезать минимальное количество образцов, испытанию подвергается 2 и более контрольных соединений. При необходимости допускается удалять усиление шва. В образцах на обоих концах сварного шва делаются надрезы глубиной до 5 мм.
При односторонней сварке шва без подкладки половину образцов следует изгибать, прикладывая нагрузку со стороны корня шва, а другую половину - со стороны усиления шва.
Рисунок 1. Схемы вырезки (а), виды (б, в) и схемы испытаний на излом со стороны корня шва (г) и со стороны усиления шва (д) образцов из стыковых контрольных сварных соединений листов
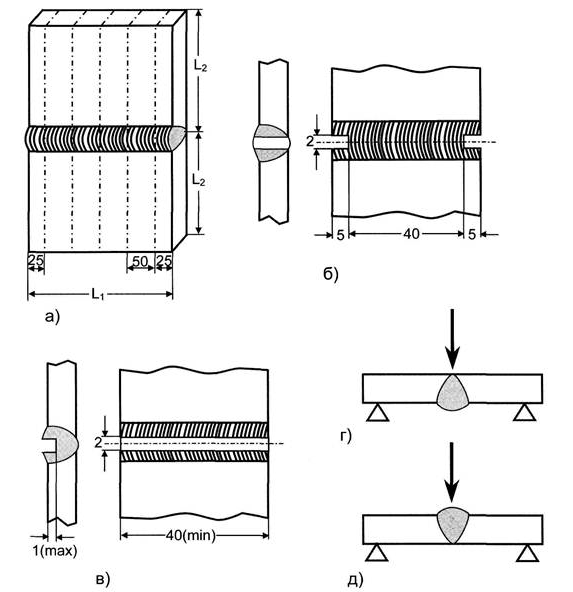
Рисунок 2. Схема вырезки (а) и испытаний (б) на излом образцов из таврового контрольного сварного соединения листов
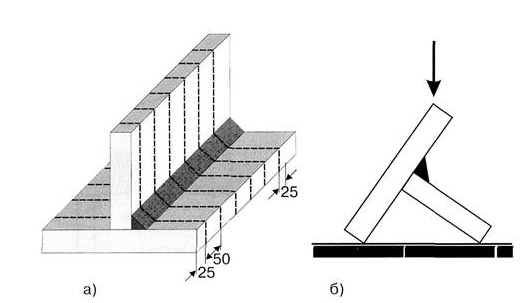
Рисунок 3. Схемы вырезки (а), вид (б) и схемы испытаний на излом со стороны корня шва (в) и со стороны усиления шва (г) образцов из стыкового контрольного сварного соединения труб
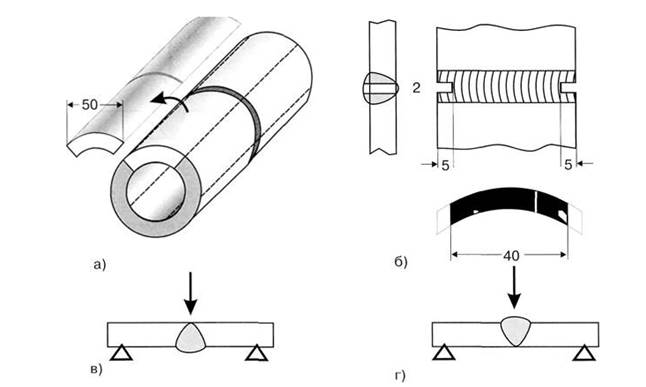
Приложение 15
к Правилам аттестации сварщиков
и специалистов сварочного
производства
Механические испытания контрольных сварных стыковых соединений из полимерных материалов
1. Испытания контрольных сварных стыковых соединений выполняют на образцах-лопатках типа 2 по ГОСТ 11262 «Пластмассы. Методы испытания на растяжение».
2. Образцы изготавливают механической обработкой из отрезков сварных соединений длиной не менее 160 мм. Допускается для труб с номинальной толщиной до 10 мм включительно вырубать образцы штампом-просечкой.
3. Из каждого контрольного сварного соединения вырезают (вырубают) равномерно по периметру шва не менее пяти образцов.
При изготовлении ось образца параллельна оси трубы. Толщина образца равна толщине стенки трубы. Сварной шов располагается посередине образца с точностью ± 1 мм. Образцы не имеют раковин, трещин и других дефектов.
4. Испытания проводят при скорости раздвижения зажимов испытательной машины, равной 100 (±10) мм/мин для образцов труб с номинальной толщиной стенки менее 6 мм и 25 (±2,0) мм/мин для образцов труб с номинальной толщиной стенки 6 мм и более.
5. Испытание на растяжение производят на любой разрывной машине, обеспечивающей точность измерения нагрузки с погрешностью не более 1 % от измеряемого значения, мощность которой позволяет разорвать образцы (усилие от 5000 до 10000 Н) и которая имеет регулируемую скорость.
6. При испытании определяют характер (тип) разрушения образца, а также предел текучести при растяжении и относительное удлинение при разрыве.
7. Критерием качества сварного соединения, выполненного сваркой встык, является характер разрушения образцов.
Различают три типа разрушения:
тип I - наблюдается после формирования «шейки» - типичного сужения площади поперечного сечения образца во время растяжения на одной из половин испытываемого образца. Разрушение наступает, как правило, не ранее чем при достижении относительного удлинения более 50 % и характеризует высокую пластичность. Линия разрыва проходит по основному материалу и не пересекает плоскость сварки;
тип II - отмечается при достижении предела текучести в момент начала формирования «шейки». Разрушение наступает при небольших величинах относительного удлинения, как правило, не менее 20 и не более 50 %, и характеризует низкую пластичность. Линия разрыва пересекает плоскость сварки, но носит вязкий характер;
тип III - происходит до достижения предела текучести и до начала формирования «шейки». Разрушение наступает при удлинении образца, как правило, не более 20 % и характеризует хрупкое разрушение. Линия разрыва проходит точно по плоскости сварки.
8. Результаты испытания считаются положительными, если при испытании на осевое растяжение не менее 80 % образцов имеют пластичный характер разрушения I типа. Остальные 20 % образцов имеют характер разрушения II типа. Разрушение III типа не допускается.
Рисунок 1. Схема вырезки образцов из контрольного сварного соединения для испытания на осевое растяжение
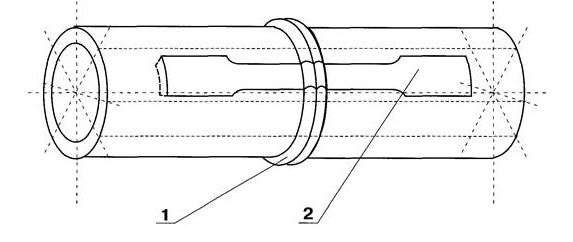
Примечание:
1 - патрубок со сварным соединением; 2 - расположение образцов.
Приложение 16
к Правилам аттестации сварщиков
и специалистов сварочного
производства
Механические испытания контрольных сварных соединений, выполненных сваркой с закладными нагревательными элементами
1. Контрольные сварные соединения, выполненные с применением муфт с закладными нагревателями, подвергают испытаниям на сплющивание. Испытания проводят на образцах-сегментах (рисунок 1 настоящего приложения) путем сжатия концевой части образца у торца соединения до величины, равной двойной толщине стенки соединяемой трубы.
Схема испытания показана на рисунке 2 настоящего приложения.
Длина выступающей части образца и количество образцов, изготавливаемое из каждого контрольного соединения, соответствует таблице 1 настоящего приложения.
2. Для испытаний применяют механизированный пресс, обеспечивающий сближение плит со скоростью 100 (±10) мм/мин; допускается использование пресса со скоростью сближения плит 20 (±2) мм/мин.
Допускается проведение испытаний с использованием обжимных плит без округления кромок. В этом случае в начале испытания расстояние от торца соединительной детали до торца губок 20 (±3) мм.
3. После снятия нагрузки образец извлекают из пресса и визуально осматривают, определяя наличие отрыва трубы от муфты или соединительной детали.
4. Стойкость сварного шва к сплющиванию характеризуется процентом отрыва Сс (%), который является отношением длины сварного шва, не подвергнувшейся отрыву, к полной длине сварного шва в пределах одной трубы
Cc = y/e × 100 %
где, y - длина шва, не подверженная отрыву, e - длина зоны сварки (длина шва) в пределах одной трубы, определяемая по расстоянию между крайними витками спирали закладного нагревательного элемента.
5. Результаты испытаний считают положительными, если на всех испытанных образцах отрыв не наблюдался или если Сс составляет не менее 40 %.
6. Сварные соединения труб и седловых отводов с закладными нагревателями подвергают испытаниям на отрыв.
Испытательная машина снабжена оснасткой, обеспечивающей приложение нагрузки по одной из двух схем испытания, приведенных на рисунке 3 настоящего приложения. Длина полиэтиленовой трубы контрольного сварного соединения принимается равной длине седелки.
Внутрь полиэтиленового патрубка испытываемого образца для передачи усилия вводят металлический сердечник, наружный диаметр которого D определяется по таблице 2 настоящего приложения, в зависимости от наружного диаметра трубы d и стандартного размерного отношения SDR.
Сварной узел подвергают испытанию целиком и нагружают до полного отделения седлового отвода от трубы.
7. Качество оценивают по виду излома в месте сварки седлового отвода с трубой. Излом имеет вязкий характер разрушения по замкнутому периметру сварного шва. Хрупкое разрушение сварного шва не допускается.
Рисунок 1. Общий вид образцов-сегментов
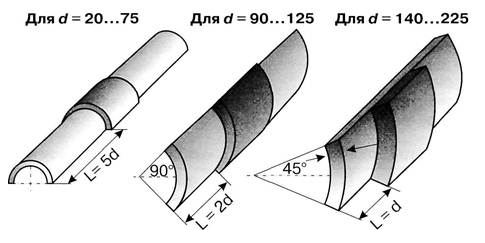
Рисунок 2. Схема испытания на сплющивание
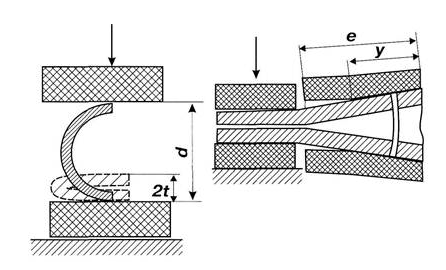
Таблица 1
Размеры образцов для испытания сварных соединений на сплющивание
Диаметр труб, d, мм | Длина свободной части образца, L, мм, не менее | Количество образцов из одного патрубка, шт. | Угол сегмента, град. |
20-75 | 5d | 2 | 180 |
90-125 | 2d | 4 | 90 |
140-225 | 1d | 8 | 45 |