Таблица 6
Предельные величины износа рельсов путей опорных и подвесных кранов при эксплуатации
Характеристика износа | Графическое представление износа | Величина допустимого износа |
Износ головки рельса (вертикальный, горизонтальный или приведенный (вертикальный плюс половина горизонтального) P6, % | 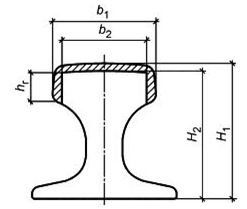 | Не более 15 от соответствующего размера неизношенного профиля (таблица 7 для стандартных типов рельсов) |
| 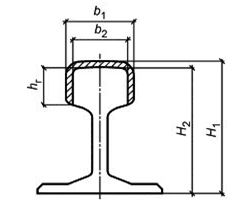 | |
Уменьшение ширины пояса двутавра ∆B вследствие износа P7, мм | 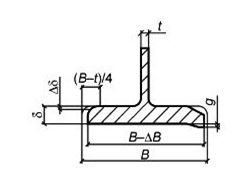 | ∆B ≤ 0,05B |
Уменьшение толщины полки двутавра ∆δ вследствие износа P8, мм | ∆δ ≥ 0,2 δ при одновременном отгибе полки g ≤ 0,15 δ |
Отгиб g полки двутавра P9, мм | ∆δ ≥ 0,25 δ при одновременном отгибе полки g ≤ 0,1 δ |
Уменьшение толщины t стенки двутавра P10, мм | не более 0,03 t |
Таблица 7
Минимальные величины размеров изношенных рельсов в миллиметрах
Тип рельса | b1 | H2 | hr | Приведенный износ |
Р43 | 59,5 | 133,7 | 42 | 10,5 |
Р50 | 61,2 | 145,7 | 42 | 11 |
Р65 | 63,75 | 173,25 | 45 | 11,5 |
Р75 | 61,3 | 183,75 | 55 | 12 |
КР80 | 73,95 | 124,75 | 35 | 10,5 |
КР100 | 918 | 140 | 40 | 12 |
КР120 | 109,65 | 163,25 | 45 | 14,5 |
КР140 | 127,5 | 162,5 | 50 | 16,5 |
Приложение 12
к Инструкции по проведению обследования
технического состояния башенных кранов с
истекшим сроком службы с целью определения
возможности их дальнейшей эксплуатации
Метод отбора проб (образцов) для определения химического состава и механических свойств металла
1. Для проведения химического анализа металла основных несущих элементов с целью стандартного определения марки стали от каждого элемента обследуемого узла берут на анализ от 20 до 30 г стружки.
2. При сложности отбора указанного количества металла могут быть использованы опытные методы, при которых объем отбираемого металла может составлять 15-20 мм3 при площади образца не менее 5 мм2.
3. Место, с которого берется стружка, предварительно очищается от пыли, грязи, смазочных материалов и зачищается до металлического блеска. Стружка отбирается засверливанием отверстия при температуре не ниже плюс 10°С. Диаметр сверла d=5-8 мм, но не более полуторной толщины элемента (листа, профиля, трубы) анализируемого узла. Расстояние между отверстием и краем элемента не менее 5d (как правило, не менее 25 мм).
В тех случаях, когда температура окружающего воздуха ниже плюс 10 °С, отбор стружки для анализа необходимо выполнять с подогретой до указанной температуры поверхности металла.
4. Место, откуда взята стружка, подлежит восстановлению с применением сварки до пуска крана в работу, о чем делается отметка в журнале осмотров, технических обслуживаний и ремонтов крана, а чертеж восстановления элемента металлоконструкции после взятия пробы хранится наравне с паспортом.
5. Отобранная стружка упаковывается, маркируется, составляется ведомость с указанием места взятия стружки (узла, элемента) марки крана, его заводского и регистрационного номеров.
Химический состав стружки определяется в соответствии с требованиями ГОСТ 22536.0-87 «Сталь углеродистая и чугун нелегированный. Общие требования к методам анализа», ГОСТ 22536.1-88 «Сталь углеродистая и чугун нелегированный. Методы определения общего углерода и графит», ГОСТ 22536.2-87 «Сталь углеродистая и чугун нелегированный. Методы определения серы», ГОСТ 22536.3-88 «Сталь углеродистая и чугун нелегированный. Методы определения фосфора», ГОСТ 22536.4-88 «Сталь углеродистая и чугун нелегированный. Методы определения кремния», ГОСТ 22536.5-87 «Сталь углеродистая и чугун нелегированный. Методы определения марганца».
6. Определение механических свойств (предела текучести, временного сопротивления разрыву, относительного удлинения, ударной вязкости) производится из проб, вырезанных из элементов металлоконструкций, подлежащих проверке.
Наиболее приемлемым методом отбора металла для определения его механических свойств из листовых конструкций является вырезка заготовки в виде круга (блина) (рисунок 1). Вырезка заготовки выполняется механическим путем (дрелью со специальной насадкой) или газовой резкой ацетиленовым или пропан-бутановым пламенем с обеспечением отсутствия пережога или перегрева вырезаемой заготовки. Из получаемой заготовки изготавливают два плоских образца I для определения предела текучести, временного сопротивления разрыву и относительного удлинения в соответствии с требованиями приложения 3 ГОСТ 1497-84 «Металлы. Методы испытаний на растяжение» (тип 1 или 2).
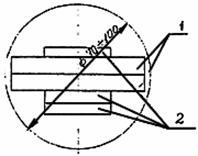
Рисунок 1. Образец круглой заготовки из листовой конструкции
Из этой же заготовки вырезают также три образца 2 для определения ударной вязкости. Образцы вырезают в соответствии с требованиями ГОСТ 9454-78 «Металлы. Метод испытания на ударный изгиб при пониженных, комнатной и повышенных температурах». Образцы испытывают при минимальной температуре эксплуатации крана.
Отбор проб в трубчатых конструкциях (секции башен, верхний пояс секций стрел, несущие пояса оголовка) производится следующим образом: например, из трубы несущего пояса 140х10 мм вырезается заготовка (рисунок 2) с закруглениями диаметром 60мм. Длина заготовки 120 мм.
Из нижних несущих поясов стрелы стандартные заготовки металла для проверки механических свойств не вырезают, ввиду невозможности восстановления конструкции без снижения ее прочностных свойств.
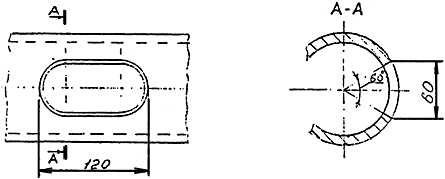
Рисунок 2. Заготовка из трубчатой конструкции
Из полученной заготовки размером 120х60 мм изготавливают (рисунок 3) полосы шириной 16 мм (две штук) и шириной 9 мм (две штуки). Из двух первых полос для определения предела текучести σт, временного сопротивления σв и относительного удлинения δ изготавливают два образца на растяжение по ГОСТ 1497-84 «Металлы. Методы испытаний на растяжение» (рисунок 3):
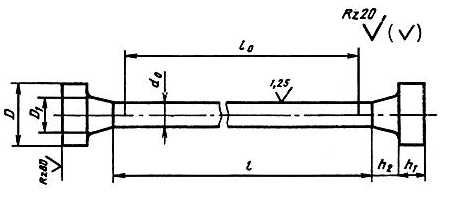
Рисунок 3. Образец заготовки для испытания на растяжение
Из двух других полос изготавливают три образца для определения ударной вязкости при температуре минус 40 °С (краны исполнения У - умеренный климат) или минус 60 °С (краны исполнения ХЛ - холодный климат) согласно требованиям ГОСТ 9454-78 «Металлы. Метод испытания на ударный изгиб при пониженных, комнатной и повышенных температурах» черт. 1, вид концентратора U, тип образца 7.
Таблица 1
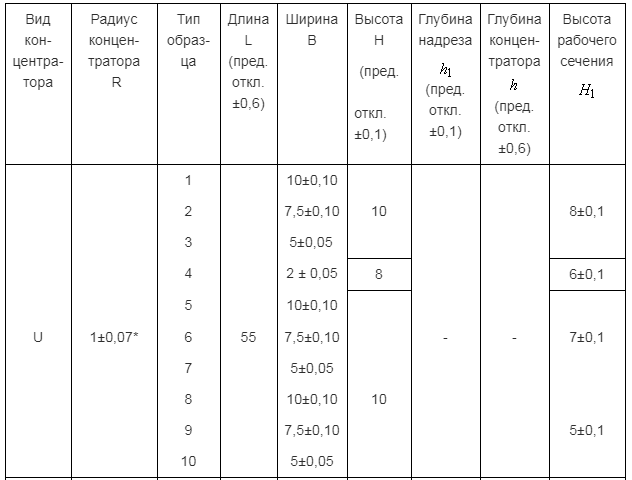
Места вырезки заготовок восстанавливаются без снижения несущей способности конструкции с выполнением требований, записанных в пункте 1 настоящего приложения:
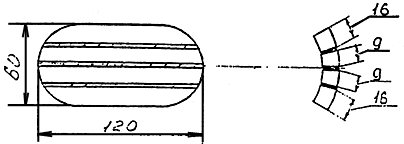
Рисунок 4.
Приложение 13
к Инструкции по проведению обследования
технического состояния башенных кранов с
истекшим сроком службы с целью определения
возможности их дальнейшей эксплуатации
Расчет металлических конструкций и деталей механизмов крана на усталость
1. Исходные данные для расчета механизмов крана на усталость соответствуют данным, указанным в конструкторской и эксплуатационной документации на кран.
Геометрические характеристики крана определяются по проектной геометрической схеме его конструкции без учета деформаций.
2. При расчете несущей металлической конструкции крана на усталость учитывается наибольшее возможное в пределах данной группы режима работы крана число циклов его работы с наибольшей массой груза, определяемое по формуле:
Ni = Np×Кq., где
Np - расчетное число циклов работы крана;
Кq - расчетный коэффициент нагрузки крана.
Предполагается, что остальные циклы работы крана, число которых Np - Ni , совершают без груза. Эти циклы учитываются только при расчете элементов, расположенных ниже опорно-поворотного устройства.
Группа режима работы крана, расчетное число циклов работы крана и расчетный коэффициент нагрузки крана устанавливается по таблице 1 настоящего приложения.
Таблица 1
Коэффициент нагрузки крана
Расчетный коэффициент нагрузки крана Кq | Группа режима работы крана при расчетном числе циклов Np |
6,3 х 10 4 | 1,25 х 10 5 | 2,5 х 10 5 | 5,0 х 10 5 | 1,0 х 10 6 | 2,0 х 10 6 |
0,125 | 1К | 2К | 3К | 4К | 5К | 6К |
0,250 | 2К | 3К | 4К | 5К | 6К | 7К |
0,500 | 3К | 4К | 5К | 6К | 7К | 8К |
1,000 | 4К | 5К | 6К | 7К | 8К | 8К |
Примечание: расчетное число циклов работы крана Np принимают по конструкторской и эксплуатационной документации и округляют до ближайшего большего значения, указанного в таблице 1.
3. При расчете деталей механизмов, усталость которых определяется циклами напряжений, обусловленными вращением рассчитываемых деталей, учитывается только наибольшее возможное в пределах данной группы режима работы механизма время его работы Т в часах с нормативной нагрузкой, определяемое по формуле:
Т = Тр×Кр, где
Тр - расчетное общее время работы механизма, ч;
Кр - расчетный коэффициент нагрузки.
Группу режима работы механизма, расчетное общее время его работы и расчетный коэффициент нагрузки устанавливают по таблице 2 настоящего приложения.
Таблица 2
Коэффициент нагрузки крана
Расчетный коэффициент нагрузки Кр | Группа режима работы крана при расчетном общем времени работы механизма Тр,ч |
0,8 х 10 3 | 1,6 х 103 | 3,2 х 10 3 | 6,3 х 10 3 | 12,5 х 103 | 25,0 х 103 | 50,0 х 103 |
0,125 | 1М | 1М | 1М | 2М | 3М | 4М | 5М |
0,250 | 1М | 1М | 2М | 3М | 4М | 5М | 6М |
0,500 | 1М | 2М | 3М | 4М | 5М | 6М | 6М |
1,000 | 2М | 3М | 4М | 5М | 6М | 6М | 6М |
Примечание:
1) расчетное общее время работы механизма принимают по конструкторской и эксплуатационной документации и округляют до ближайшего большего значения, указанного в таблице 2;
2) под временем работы механизма принимают время, в течение которого механизм находится в движении (действии).
4. При расчете деталей механизмов, усталость которых определяется циклами напряжений, обусловленными изменением крутящего момента, число циклов изменения крутящего момента N2 принимается не менее значений, указанных в таблице 3.
Таблица 3
Число циклов изменения крутящего момента
Наименование механизмов | N2 |
Механизмы подъема груза и стрелы | 1,2 N1* |
Механизмы поворота | |
кранов с балочной стрелой | 600 Тр |
кранов с подъемной стрелой | 1000 Тр |
Механизм передвижения груза тележки | 200 Тр |
Механизм передвижения: | |
кранов с балочной стрелой | 600 Тр |
кранов с подъемной стрелой | 1000 Тр |
* - N1 - число циклов работы крана с наибольшей массой груза за время работы рассчитываемого механизма.
Примечание: допустимое уменьшение числа N2: для механизма поворота в 2 раза, если предусмотрена фиксированная частота вращения крана, обеспечивающая скорость точки подвеса при максимальном вылете не более 0,3 м/с; для механизма передвижения - в 2 раза, если привод имеет не менее, чем три пусковых ступени управления и, дополнительно в 2 раза, если он не содержит червячных или глобоидных передач.
5. При расчете сварных элементов металлических конструкций и деталей механизмов на усталость расчетное сопротивление усталости принимается с учетом полноты контроля сварных соединений радиографическими или другими физическими методами.
Также, полноту контроля сварных соединения возможно определить с помощью коэффициента КК, понижающего сопротивления усталости и принимаемого по таблице 4.
Для основного металла вдали от сварного шва и для несварных соединений КК = 1.
Таблица 4
Число циклов изменения крутящего момента
Вид сварного соединения | Длина контролируемого шва, % от полной длины шва | КК |
Стыковое соединение, расположенное перпендикулярно или под углом к действующему усилию | 100 | 1,0 |
25 | 0,8 |
Стыковое соединение, расположенное параллельно действующему усилию | 25 | 1,0 |
Угловое соединение | 25 | 1,0 |
0 | 0,8 |
Приложение 14
к Инструкции по проведению обследования
технического состояния башенных кранов с
истекшим сроком службы с целью определения
возможности их дальнейшей эксплуатации
Балльная шкала оценок дефектов и повреждений металлических конструкций
Наименование дефекта, повреждения | Оценка, n баллов |
дефекты и повреждения, возникшие |
при монтаже, перевозке | при работе крана |
1. Первичная трещина по сварному соединению (шов, околошовная зона): |
в поясах, коробчатых конструкциях | 1,25 | 2,5 |
в связях*, ребрах | 0,5 | 1,0 |
2. Первичная трещина по основному металлу: |
в поясах, коробчатых конструкциях | 1,75 | 3,5 |
в связях, ребрах | 0,75 | 1,5 |
3. Первичная деформация элементов, превышающая нормативные данные: |
стрелы или башни (в сборе), пояса | 2,5 | 5,0 |
связи | 0,5 | 1,0 |
листовой конструкции | 1,25 | 2,5 |
4. Выработка (износ, смятие) отверстий сверх предельных значений по настоящей Инструкции | 1,0 | 2,0 |
5. Коррозия: | | |
50-95 % от предельной величины | - | 1,0 |
при достижении предельной величины | - | св. 5,0 |
6. Расслоение металла | свыше 5,0 | св. 5,0 |
7. Повторные дефекты по пунктам 1-5 | 1,3 n | 2 n |
Примечание: *под «связями» понимаются элементы, связывающие пояса между собой в решетчатых конструкциях (раскосы, диагонали, стойки, связи).